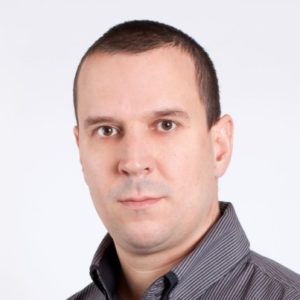
Jarda
Forum Replies Created
-
Hi,
If I understand right, when you mechanically do some force to the housing, relay is connected?
It looks as some interconnection problem inside the device. If it is so, please contact the seller and do the reclamation.
BR
Jarda
-
Hello Markus,
could you please be more specific about what exactly is not working? Please check the proper connection of A and B signals. Also please check the RS485 termination resistor – this shall be done externally. Also check the communication speed and all commands.
Sometimes it is good to use some USB-RS485 converter and try it via PC so you are sure that you fully understand the communication and the PoStep is working and then connect the Controllino.
BR
Jarda
-
Dear Alex,
CONTORLLINO MAXI Automation shall be able to delivery 0-10V on the output (resistor 500 Ohms is internally inside the CONTORLLINO to GND as default. So you shall get the voltage on the output.
Yes, DIM+ shall be connected to AO0 or AO1 and DIM- to GND. Please try to measure the voltage on this pin via Multimeter.
Regards
Jarda
-
Hello Alex again,
now I’m reading that you are using D15, so you dont have CONTROLLINO Automation and you HAVE MEGA, so you are using PWM control. Sorry for my mistake 😉
Yes, load resistor helps in your case, maybe you can go little bit lower to for example 10K, because current at meanwell power supply is in uA so maybe because of internal capacitance there is still some voltage.
I hope you have version of the power supply for PWM, not for DALI ;-).
Also please note, that PWM input of the meanwell power supply shall be around 10V, so dont use your controllino at 24V 😉
Next point is, that Meanwell power supply needs around 1.5kHz the PWM, it is on the border of possibilities of CONTROLLINO output. So probably output is not able to achive this frequency and on the ouput is “only” the voltage, not PWM. Please check it via oscillocope.
Best Regards
Jaroslav
-
-
Hello Franz Wegerer,
If you are using Half-Bridges – CONTROLLINO MEGA, there is internally freewheeling diode because of low side transistor internal body diode – no need to connect it externally.
The problem is probably following. Because your motor is turning ON on the full speed, and you want to switch it OFF, you set both low side transistors to short circuit and motor is for the short time working as a generator and it generates such high current, that is detected as over-current inside the CONTROLLINO and reported as overload. This functionality with both transistors to low side is used for hard brake of the motor.
If you don’t need the hard brake, switch it OFF in the way that for short time you switch OFF only the high side transistor and then ON the low side (play with proper timing in your application).
Best Regards
Jarda
-
Hello Everaerta,
unfortunately you cannot change the direction of rotation with Controllino MINI. Digital output internally contains only high side switch connecting the load (motor in your case) to input voltage. If you want to connect the motor and change the rotation direction, use Controllino MEGA, it has Half H-Bridge for such purposes.
Via potentiometer you can regulate the rotation speed, but you will have power looses on this potentiometer when connected in series with the motor. For better control of the speed you can use PWM modulation on the output and use for example potentiometer for MINI analog input and do the regulation in Software (transfer internally voltage information from analog input to PWM digital output.
Also please note, that digital output of the controllino MINI has nominal current of 2A. If you are using motor with 4A, digital output can be switch OFF because of overload.
Have a fine day and thank you for using CONTROLLINO.
Jarda
-
Hello Calvin,
the ports are there to simplify your cable harness if needed (for example you can continue from this ports to power other CONTROLLINO, use this port as common GND and power point, etc.). The ports are identical and are fully interconnected together.
Note: please take care, how you are measuring it, when the screws are not fully screwed, screw from the the top side has no contact. Try to fully screw and measure again ;-).
BR
Jarda
-
Hello,
I’m sorry for late reply. It looks as a wrong device, did you send it for reclamation?
BR
Jarda
-
Hello Frank,
thank you for interesting about our CONTROLLINO. Datasheet of used relays specifies Maximum allowable DC voltage to 300 VDC. So in general yes, you can use it for 60V but not for the full current of 16A. Relay is specified to max. 480W switching power which is for applied 60V 8A only.
Is this please suitable for you?
BR
Jarda
-
Hi JamesC,
Serial1 is also used for USB programming and communication with PC when USB is connected. Maybe this can be the issue.
BR
Jarda
-
Hello Tom,
for which design tool you need the electric scheme?
BR
Jarda
-
Dear Alex,
D14 output is High side switch, so that means it doesn’t go to zero and you shall have significant load for proper operation.
Also PWM can be problem with inductive load types without freewheeling diode.
What type of load do you have please? 1kOhm in parallel to dimmer can work. What exact type of dimmer do you have please? If it has analog input, you shall have some rectification also to the dimmer.
Thank you !
BR
Jarda
-
This reply was modified 3 years, 9 months ago by
Jarda.
-
This reply was modified 3 years, 9 months ago by
-
Hello Calvin,
I’m part of the CONTROLLINO Helpdesk team.
I hope your email will be replied soon.
BR
Jarda
-
Hello,
thank you for feedback, we will do our best to improve it. For 5V encoder interface you can use pins at the pinheader.
BR
Jarda